Everything you need to know about perforated metal
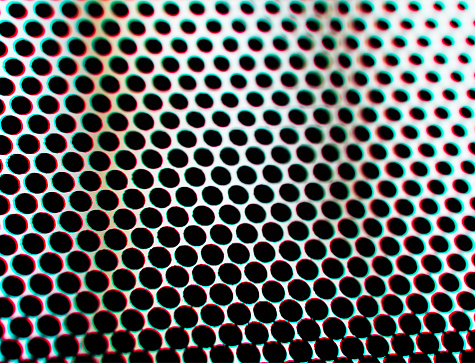
Sefar is the largest supplier of perforated metals in Australia and New Zealand, offering a wide range of perforation patterns, perforated metal screens and related products available in stock in our warehouses. Perforated metal is used across a variety of industries including Food & Beverage, Chemicals, Mining, Construction and Interior Design. The choice of metals, width, thickness, hole size and shape is determined by the use to which the perforated metal will be put. For instance, perforated metal with very fine holes is often used in filtration or screening applications. Each application calls for a specific perforation pattern.
At Sefar, we have a significant experience in the industrial processing in Chemical, Pharmaceutical, Wastewater and Mining industries. From small, high-precision perforation in thin materials to large holes in thick sheets utilised in the mining industry, we have the ability to provide you with the product you need.
We have also a broad experience in food processing. Perforated screens are used for holding or screening of food products due to its broad range of useful qualities. The first requirement for any material used within the food industry is exceptional cleanliness and hygiene.
Custom perforated solutions for food production environments are ideal for cleaning, heating, steaming and draining food products during the preparation. In cereal processing, perforated metals are used for screening raw grains and removing unwanted materials mixed with the grains. They gently and thoroughly remove dirt, shells, stones, and small bits from corn, rice, and legume, to name a few. Its popularity is due to its affordability, lightness, strength, durability, versatility and practicality. However, before we check out the different types and applications of perforated metal mesh, let’s take a look at how it’s manufactured.
What is perforated metal?
Perforated metal is made from sheets of stainless steel, aluminium, mild steel or galvanised mild steel. The sheets need to be flat and thin enough to be cut and perforated easily. The application of the final product will determine the type and size of the pattern that’s perforated into the metal sheet.
The larger and more numerous the perforations, the less strength is left in the sheets. So applications where strength is a priority require smaller and fewer perforations. These requirements help you decide on the pattern for the perforations which can be round, square, slotted, decorative, hexagon or custom designed.
- Round perforations: These perforations can be made in straight
lines so they are parallel and perpendicular to each other. They can
also be staggered so they are out of alignment. Round perforations
are very popular and a traditional pattern that’s used extensively
across industries. - Square perforations: These are a more modern and up-to-date
pattern that provides a design with more open space than round
perforations. They can also be in a linear or staggered pattern. - Slotted perforations: These are oblong or tablet shaped
perforations that can be linear or staggered. Slotted designs are
extremely strong and allow more air, light and noise to pass through
than round or square perforations. - Decorative perforations: These tend to be more aesthetic than
functional and are very popular with architects and interior
designers. We have a wide variety of popular decorative design
templates that can be cut to fit your application. - Hexagon perforations: These perforations have the highest
amount of open space and allow the greatest amount of air, light
and noise through the mesh. They are used almost exclusively by
architects and interior designers, because their application is
aesthetic rather than functional.
The sheet metal used at Metal Mesh to create all of these perforations is premium quality sourced from Europe and results in a burr free final product. In addition, we can provide your perforated metal in flat sheets, rolls, strips or any other shape that suits your requirements.
What are the different types of perforated metal mesh?
At Metal Mesh we provide six different types of perforated Metal, which should cover all your construction and design needs. All are available in 2000 x 1000mm or 2500 x 1250mm flat sheets and you can select from thousands of stock patterns available in our factory, as well as custom designs.
- Perforated Aluminium is commonly used in interior fit outs, air vents, running boards, lighting, water treatment applications, partition walls, railings and much more.
- Perforated Mild Steel is commonly used in screens, shelving, racks, washer plates, air vents and so on. It’s easy to cut and is stronger than aluminium.
- Perforated Stainless Steel is used where strength is a priority, for example in safety flooring or decks. Heavier than its aluminium equivalent, perforated mild steel is also stronger, as well as rust resistant.
- Perforated & Decorative options are available in mild steel, aluminium or anodised aluminium. Commonly used in architectural and interior design applications.
- Perforated Galvanised Mild Steel is used for the same applications as mild steel except that it’s given a protective coat of zinc prior to perforation. Commonly used in landscaping, architectural designs, outdoor security fencing, exterior furniture or anywhere a mix of strength and decoration is required.
- Perforated Processing Screens are made from stainless steel. Commonly used in agriculture as grain cleaning and drying screens, malting floor screens, rice sorting screens, and so on.
Perforated metal vs woven wire mesh vs welded wire mesh
Understanding the differences among these meshes helps you decide which is best for your project.
Perforated metal mesh: This is produced by punching the design into metal sheets to create a pattern of holes in the metal. It’s ideal for industrial and food processing depending on the type of metal sheet and
the size and number of perforations.
Woven wire mesh: Woven wire mesh is produced by weaving strands of horizontal and vertical wire over and under each other, resulting in a sheet of square wire mesh. It’s ideal for sifting and screening, as well as architectural applications.
Welded wire mesh: Welded wire mesh is produced by welding an array of metal wire from different spools into cross wires at the required spacing to form metal wire screens. It’s ideal for fishing traps, catwalks, fencing, cages and concrete reinforcement.
Benefits of using perforated metal
Depending on the type of metal sheeting used and the size and density of the holes, perforated metal can be used for a wide range of applications. That’s because this type of product has a number of interesting benefits for a variety of projects.
- Aesthetic Advantages for Metal: The most important features are their ability to filter natural light, create a pleasant and satisfying appearance, and provide a space for air circulation.
- Versatility of Perforated Metals Part of the versatility of perforated metals is their ability to be bent, shaped, and configured to meet the needs of an application and design. The many uses for perforated metals include sound suppression, infills for railings, barriers above and below railings, covers for columns, filtration for fluids and light, and coverings for windows.
- Lightness: Perforated metal mesh is easier to work with and lighter than non-perforated equivalents and also places less stress on the structure of a building or interior fixture.
- Strength: Despite the holes, perforated metal meshes are still very strong. For optimal strength, a standard 60 degree staggered pattern of perforations is recommended.